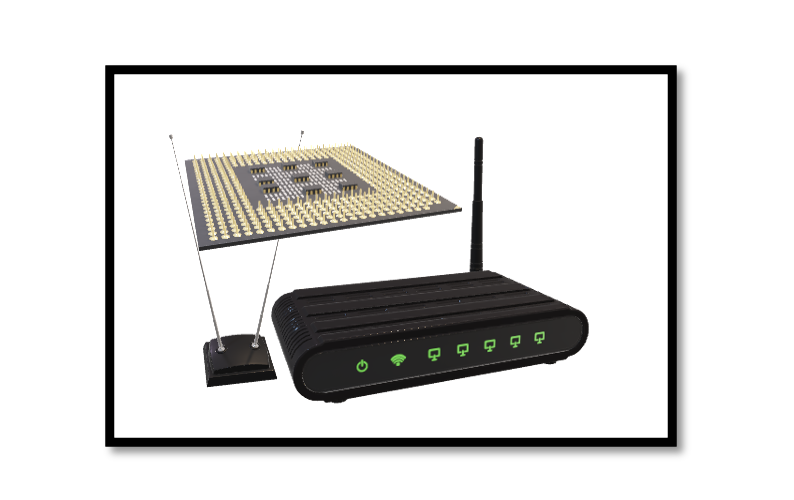
Factory Testing in RF Devices: Ensuring Quality in Electronics
Understanding Factory Testing
Factory testing is the culminating stage in electronic device manufacturing. Also termed as final testing, this critical phase ensures the quality and functionality of products before they reach consumers. It’s the last line of defense against faulty devices hitting the market.
At its core, factory testing encompasses a suite of examinations performed at the manufacturing site. This process, also known as final testing, strives to ascertain that every device leaving the production line is not just a shell but a fully functional, high-quality product. Picture this: You purchase a smartphone, eagerly unbox it, only to find that crucial functionalities like Wi-Fi or calling features fail to work. It’s a consumer’s nightmare and a manufacturer’s detriment—a scenario swiftly avoided through meticulous factory testing.
Necessity in Quality Assurance
By sidestepping factory testing, a company inadvertently invites a deluge of customer returns. Perfection, in manufacturing, is a distant dream, but striving for it remains the hallmark. This final assessment, often following various preceding evaluations such as optical inspections, X-rays, in-circuit testing, and visual inspections, aims to deliver a product that meets or exceeds consumer expectations.
The overarching goal of factory testing is to ensure products are fully operational before they leave the facility. This necessitates optimizing test times, striving for efficiency in mass production, and, significantly, considering the implications of the testing process on the manufacturing and design phases.
Scope and Objectives
- Purpose: Ensuring products are fully operational pre-distribution.
- Optimization Goals: Focus on reducing test times for mass production efficiency.
- Influence on Design and Manufacturing: Acknowledging the impact of testing on the earlier stages of product development.
What to Test and What to Skip?
- What to Test: Identifying crucial test components.
- Test Coverage Analysis (TCA): Evaluating testing breadth and redundancy from prior processes to optimize final RF testing.
A crucial inquiry within factory testing is discerning what to examine rigorously and what to bypass. Test Coverage Analysis (TCA) emerges as a vital tool, offering insights into the testing breadth and the redundancy in prior processes, thereby optimizing the final RF testing phase.
Key Factors for Success
- Test and Cycle Time: The shorter, the better. Minimizing the duration without compromising quality or depth of testing remains pivotal.
- First Pass Yield: Aim high, aim for perfection. Reducing retests reflects robustness in the testing phase.
- Repeatability: Consistency matters. Ensuring that measurements and processes are reproducible is integral.
- Statistics: Insights into process behavior guide improvements and adjustments.
- Simplicity: Avoid complexity where possible. Simple tests often ensure higher repeatability and lower test times.
- Automation: Embrace efficiency. Automating tests and handling procedures streamlines processes and reduces human error.
- Handling: Proper care translates to fewer errors. Mishandling can impact both yield and cycle time.
Design for Manufacturing: Bridging the Gap
For designers, understanding factory testing becomes paramount. Aligning the design aspects with manufacturing requirements paves the way for a smoother production journey. The feedback loop created by final testing echoes through the entire product lifecycle, influencing future designs and production strategies. In the intricate world of RF testing, the final frontier of quality assurance is crafted in the meticulous embrace of factory testing. Its significance not only lies in ensuring product functionality but also in serving as the compass guiding the interplay between design precision and manufacturing excellence.
Technology Advancements in Factory Testing The evolution of technology has revolutionized factory testing methodologies. Advanced tools like Automated Test Equipment (ATE) and sophisticated software have streamlined testing processes. With the advent of AI and machine learning, predictive maintenance and adaptive testing algorithms have emerged, enhancing accuracy and reducing test times.
Importance of Test Validation and Calibration Validating and calibrating test equipment regularly is paramount. Rigorous validation ensures that the testing instruments are accurate and consistent. Calibration guarantees that measurements adhere to standards, maintaining the integrity of the testing process and the reliability of results.
Environmental Considerations in RF Testing RF devices are sensitive to environmental factors. Conducting tests in controlled environments that mimic real-world scenarios is essential. Factors like temperature, humidity, and electromagnetic interference can significantly impact the performance of RF devices, warranting thorough testing under various conditions.
Collaboration Across Departments for Optimal Testing Effective factory testing necessitates collaboration among various departments. Close cooperation between design, manufacturing, quality assurance, and testing teams ensures that the testing phase aligns with the intended design and addresses any production challenges, ultimately enhancing the final product’s quality.
The Role of Compliance and Regulatory Standards Meeting industry standards and regulatory compliance is non-negotiable in factory testing. Adhering to FCC regulations, industry standards such as ISO, and specific product certifications is imperative. Compliance ensures that products meet safety, quality, and performance benchmarks, fostering consumer trust.
Continuous Improvement Through Feedback Loops The data collected from factory testing creates invaluable feedback loops. Analyzing test results helps identify patterns of failure, allowing for continuous improvement in both manufacturing processes and product design. Iterative refinement based on this feedback ultimately leads to higher-quality products. By incorporating these additional sections, the blog gains depth, covering aspects such as technological advancements, environmental considerations, interdepartmental collaboration, compliance requirements, and the iterative nature of improvement in factory testing processes.
Conclusion
Factory testing in RF devices represents the culmination of meticulous efforts in ensuring the integrity and functionality of electronic products. As the final gatekeeper before devices reach consumers, its significance cannot be overstated.
From the critical assessments conducted to the optimization of test times, factory testing stands as the linchpin in the manufacturing process. It not only guarantees the functionality of devices but also serves as a bridge between the intricate design nuances and the practical realities of mass production.
The evolution of technology has paved the way for more sophisticated testing methodologies, while adherence to compliance standards and environmental considerations continues to shape the testing landscape.
However, the true essence lies in the collaborative efforts across departments, from design to testing, aimed at achieving a unified goal of delivering impeccable products to the market. The iterative nature of testing, driven by data and continuous improvement, ensures that each cycle refines the process further, aiming for excellence. In essence, factory testing in RF devices is not merely a phase; it’s an ongoing commitment to quality, an amalgamation of precision, technology, collaboration, and a relentless pursuit of perfection. It’s the assurance that every device leaving the manufacturing line embodies the standards of excellence set forth by the industry and the expectations of discerning consumers worldwide.
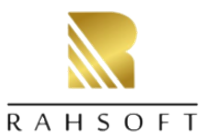
Learn more about this topic by taking the complete course ‘Introduction to RF Testing Fundamentals and RF Test Architecture – RAHRF412’. Watch the course videos for more detailed understanding. Also checkout other courses on RF system and IC design on https://rahsoft.com/courses/. Rahsoft also provides a certificate on Radio Frequency. All the courses offer step by step approach.