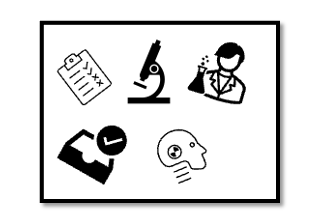
RF Laboratory Testing: An In-Depth Overview
Introduction
RF laboratory testing stands as a critical phase, a meticulous process that serves as the bedrock ensuring a product’s performance, functionality, and compliance before it ventures into mass production. This phase is where the intricate dance between innovation and validation occurs. But what exactly does it entail?
Understanding the Depth of Lab Testing
Lab testing isn’t just another step; it’s the apex of the design process. It’s the marathon where extensive testing ensures that a device operates flawlessly across diverse applications. This rigorous validation encompasses everything from design confirmation to component characterization, often spanning hours or days, contingent upon the product’s complexity.
Scope and Comprehensive Testing
At this stage, the goal is clear: scrutinize every basic and advanced feature, fortifying the design’s resilience before it steps into the bustling world of production. Stress and reliability assessments become integral—probing how RF components endure harsh environmental conditions or rigorous tests like ESD, giving insights into long-term functionality. Experimentation becomes an ally here. Running tests under diverse conditions allows for fine-tuning designs, tweaking frequencies, or optimizing component outputs. It’s the compass guiding designers to enhance performance, even in factory settings, facilitating continual improvement within the production pipeline.
Essential Considerations
Engaging in lab testing demands more than just scrutiny; it requires a suite of advanced equipment. These tools, often costly due to their sophisticated features, include vector signal generators, spectrum analyzers, or VNAs, elevating the precision and depth of evaluations.
Yet, it’s not merely about tools; it’s about expertise. In this realm, understanding the product and instrumentation becomes pivotal. Unlike factory settings, manual intervention might be necessary, scripting tests, and navigating complexities, especially in testing intricate devices like transmitters or receivers.
Moreover, the field isn’t confined to lab walls. Field testing emerges as a reality, bringing the evaluation of devices like GNSS receivers or smartphones to real-world scenarios, ensuring performance aligns with expectations in practical usage.
What to Test in the Lab
The spectrum of lab testing encompasses multifaceted assessments:
- Functional Testing: The foundational examination ensuring basic operations like measuring output power or gain in RF power amplifiers.
- Reliability Testing: Subjecting devices to varying environmental conditions, foreseeing how they withstand temperature fluctuations or other stressors.
- Electromagnetic Compatibility (EMC): Even at lower frequencies, addressing spurious emissions or harmonics is critical to compliance and optimal performance.
- Mechanical Testing: Occasionally intertwined with electronic engineering, ensuring components endure mechanical stress like vibration.
- Regulatory and Standardized Testing: Vital for wireless applications, compliance with country-specific regulations dictates the permissible power, frequency range, and emissions.
- Safety and Special Requirements: Addressing unique client demands or carrier specifications, transcending standardized testing protocols.
Optimization through Iterative Testing
Beyond the initial round of testing lies a realm of iterative refinement. Lab testing isn’t a one-time affair; it’s a cyclical process of testing, analyzing, and fine-tuning. Each test iteration brings forth a trove of data that’s meticulously analyzed, providing insights into potential enhancements. This iterative approach is the cornerstone of achieving optimal performance, ensuring that each facet of the device’s functionality is scrutinized and enhanced.
Challenges in Lab Testing
The laboratory presents its own set of challenges. While it provides a controlled environment, mimicking real-world scenarios perfectly can be a daunting task. Simulating every conceivable usage scenario or environmental condition accurately demands creative thinking and exhaustive planning. Moreover, the complexity of some devices adds layers of intricacy, requiring innovative testing methodologies to capture every nuance of performance.
Interdisciplinary Collaboration
Successful RF laboratory testing isn’t solitary; it’s a collaborative effort that transcends disciplines. Collaborations between electronics engineers, mechanical engineers, software developers, and regulatory compliance experts are crucial. This convergence of expertise ensures that every aspect of the product, from hardware functionality to software integration, is meticulously evaluated and refined.
The Role of Simulation and Modeling
Simulation and modeling stand as essential tools complementing laboratory testing. Before a physical prototype is even crafted, virtual simulations provide a playground to forecast performance, optimizing designs prior to physical manifestation. These simulations, coupled with real-time data collected during lab testing, create a robust feedback loop, streamlining the iterative refinement process.
The Imperative of Documentation and Traceability
In this phase of exhaustive testing, documentation becomes paramount. Every test conducted, data collected, and analysis performed needs to be meticulously documented and traceable. This not only ensures compliance with industry standards but also provides a roadmap for future improvements or troubleshooting.
Addressing Emerging Technologies and Innovations
As the landscape of technology evolves, so does the scope of RF laboratory testing. Emerging technologies like 5G, IoT, or advancements in satellite communication demand continual adaptation in testing methodologies. Keeping abreast of these innovations and modifying testing protocols accordingly ensures that products remain at the forefront of technological advancements.
The Evolution Towards Automation
While manual intervention remains integral in many aspects of lab testing, there’s an ongoing shift towards automation. Automated test systems streamline repetitive tasks, increase testing throughput, and enhance accuracy, reducing human error and expediting the testing process. In the labyrinth of RF laboratory testing, these nuanced layers underscore the depth and complexity of this critical phase in product development. It’s not just about validating designs; it’s about sculpting products that withstand the rigors of real-world usage, promising reliability, performance, and compliance.
Conclusion
RF laboratory testing isn’t a mere checkpoint; it’s a crucible where innovation and precision converge to sculpt products of unparalleled quality. The exhaustive scrutiny, iterative refinement, and interdisciplinary collaboration within the laboratory walls are the keystones shaping the success of devices in the real world. From meticulous documentation to navigating emerging technologies, every facet of this phase contributes to the robustness and reliability of products. It’s a testament to the meticulous efforts poured into ensuring that each device doesn’t just function but excels across diverse scenarios. As technology continues its ceaseless evolution, the laboratory remains the beacon, where products are honed, refined, and readied to meet the demands of an ever-evolving world. In this intersection of innovation and testing, the laboratory stands as the veritable birthplace of excellence.
RF Laboratory versus Factory Testing Summary: A Balanced Approach
In the sphere of RF component testing, the distinction between laboratory and factory environments brings forth a dichotomy that underscores complexity versus simplicity, intricate equipment versus streamlined solutions. Let’s encapsulate the essence of these distinct domains and explore the harmonious meeting point that propels efficient testing strategies.
Laboratory Testing: Delving into Complexity
Within the laboratory’s confines, complexity reigns supreme. The demand for sophisticated equipment arises from the necessity to validate intricate design elements and advanced features. Design validation often traverses intricate solutions that necessitate equipment capable of handling such sophisticated tests. It’s crucial to bridge the gap between design engineers, who conceive these tests, and those who implement them, often relying on automated solutions. Access to software that aids in executing complex tests becomes pivotal in this realm.
Factory Testing: Embracing Simplicity for Efficiency
Contrarily, simplicity reigns supreme in the factory setting. The focus is on minimal test items, ensuring that products are functioning optimally without overwhelming complexities. This lean approach not only expedites testing but also curtails debugging complexities, significantly impacting throughput. Simplicity and throughput become symbiotic; fewer tests directly translate to faster cycles and reduced test times, a critical factor in mass production scenarios.
Finding Harmony: Meeting Halfway
Striking a balance between the demands of laboratory and factory testing entails collaboration and strategic planning:
- Collaboration Between Engineers: Design or product engineers define test parameters, while test engineers implement these tests. Harmonizing their efforts ensures a seamless transition of tests from validation to production phases.
- Equipment: Bridging the Divide: The quest lies in finding equipment adaptable to both settings. Collaborating with equipment suppliers is pivotal; seeking solutions that require minimal upgrades to function in both environments fosters efficiency and cost-effectiveness.
- Scalability as a Guiding Principle: Embracing scalable equipment aligns testing strategies with long-term organizational roadmaps. Establishing partnerships with suppliers, leveraging their expertise to tailor solutions, ensures a seamless integration of evolving testing needs with equipment capabilities.
Conclusion: The Path to Efficiency and Adaptability
In navigating the complexities of RF component testing, the synergy between laboratory and factory testing emerges as a cornerstone of efficiency. While the laboratory dives deep into validation and complexity, the factory thrives on simplicity and throughput. The art lies in harmonizing these seemingly divergent approaches, fostering collaboration, seeking adaptable solutions, and embracing scalability. This balanced approach not only optimizes testing strategies but also fortifies adaptability, ensuring a seamless transition from design validation to mass production in the dynamic landscape of RF component testing.
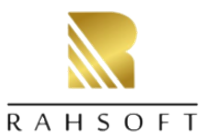
Learn more about this topic by taking the complete course ‘Introduction to RF Testing Fundamentals and RF Test Architecture – RAHRF412’. Watch the course videos for more detailed understanding. Also checkout other courses on RF system and IC design on https://rahsoft.com/courses/. Rahsoft also provides a certificate on Radio Frequency. All the courses offer step by step approach.