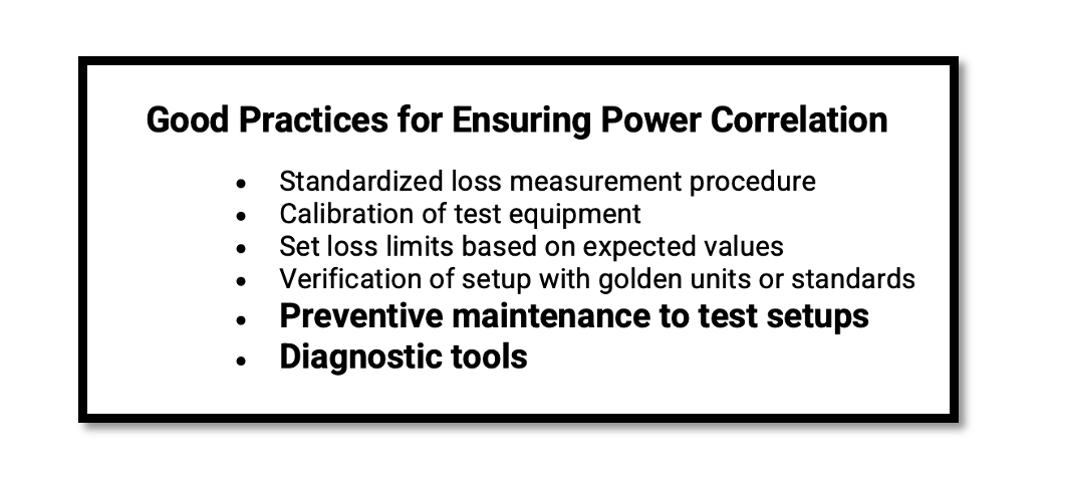
Power Correlation: The Role of Preventive Maintenance and Diagnostic Tools
Introduction:
Navigating the intricate landscape of RF power testing demands a strategic fusion of preventive maintenance, diagnostic tools, and meticulous calibration practices. As technology evolves, so does the need for precision in RF power correlation—a crucial aspect in both research and development (R&D) environments and manufacturing facilities. In this blog, we explore the synergistic relationship between preventive maintenance and diagnostic tools, shedding light on their pivotal role in reducing downtime, safeguarding equipment, and ensuring accurate measurements. Additionally, we delve into the significance of adhering to calibration schedules, introducing practices that fortify the reliability of RF power testing setups. Join us as we unravel the nuances of efficient testing practices and optimal equipment performance, ultimately enhancing the quality and reliability of RF power correlation.
Preventive maintenance to test setups
- Creating a golden unit requires accurate measurements
- Accurate equipment usually found in lab environment
- Identify the DUT and data
Diagnostic tools
- Creating reference samples is simple
- Setup can be verified with golden sample
- Allows for less golden unit handling.
Let’s delve into the realm of maintenance, where preventive measures serve as the cornerstone in numerous companies globally. Rather than waiting for test equipment to reach a critical failure point, implementing preventive maintenance becomes crucial. This proactive approach aims to circumvent inaccurate testing, the need for retests, potential equipment damage, and, most importantly, to maximize throughput. In a factory setting, equipment malfunctions can lead to downtime, hindering productivity. This practice is equally paramount in both research and development (R&D) environments, where precision is imperative. Retesting, though less impactful in R&D, can still pose significant challenges, especially when tests span hours or days. Minimizing throughput by prolonging test or cycle times is undesirable in any setting.
Equipment damage adds another layer of complexity to the importance of preventive maintenance. Consider scenarios involving the testing of high-power amplifiers or other components requiring a linear driver, as mentioned in an earlier example. In such cases, a linear driver outputs power to a component, and any issues with the setup that cause reflections may result in a damaging power return to the driver. Given the often high cost of these components, the economic implications of equipment damage underscore the need for preventive maintenance. This practice not only safeguards against financial losses but also ensures the seamless operation of high-value equipment. By adhering to preventive maintenance routines, the risk of damage is mitigated, and throughput is maximized.
In tandem with preventive maintenance, the integration of diagnostic tools becomes indispensable. These tools serve as an additional layer of defense, aiding in troubleshooting and accessible for use by anyone within the team. Automation of diagnostic tools further enhances their efficacy, streamlining the identification and resolution of issues. By proactively addressing potential problems through preventive maintenance and providing teams with robust diagnostic tools, organizations can fortify their RF power testing processes, ensuring reliability, accuracy, and optimal throughput in both R&D and factory environments.
Implementing Proactive Maintenance Strategies
Embracing a combination of preventive maintenance and diagnostic tools plays a pivotal role in curbing downtime, particularly when automation is integrated. Automated testing not only expedites the process but also furnishes precise results that aid in pinpointing failures swiftly. To ensure seamless operations, certain best practices within preventive maintenance are indispensable. One such practice involves meticulous attention to connection torque, especially when dealing with commonly used SMA connectors. Utilizing a torque wrench is paramount here, as it enables precise control over torque levels, preventing connector damage due to excessive force—an often overlooked yet critical detail. Failure to control torque might inadvertently harm connectors, leading to operational issues. Another vital practice is the regular cleaning of test equipment components. Neglecting this seemingly mundane task can pave the way for detrimental consequences. Dust accumulation, if left unattended, poses risks of equipment damage over time, potentially inducing unwanted resonances that affect Device Under Test (DUT) measurements and lead to inaccurate readings of losses. Therefore, ensuring the cleanliness of connectors, fans, and the equipment’s exterior is imperative to maintain optimal functionality and accuracy in testing procedures. Though seemingly basic, these practices are frequently overlooked, making their implementation crucial for sustained performance and reliability.
Streamlining RF Testing Efficiency: Leveraging Diagnostics and Calibration Practices
Incorporating diagnostic routines into your testing procedures can be remarkably beneficial. Many test equipment models come equipped with built-in self-tests, serving as a quick troubleshooting aid. Leveraging these diagnostics eliminates the need for separate automated solutions, as they are already provided by the equipment supplier. It’s a seamless way to ensure the equipment’s functionality without additional setups or investments.
Moreover, the synchronization of preventive maintenance and calibration dates is essential. Regularly checking calibration due dates and promptly replacing or sending out equipment for recalibration is fundamental. Maintaining a detailed calendar highlighting calibration schedules for all in-use equipment streamlines this process, ensuring no equipment exceeds its calibration date. When encountering equipment that seems out of specifications during testing, a swift substitution with spare parts and immediate arrangements for repairs or recalibration is prudent to maintain the accuracy and reliability of the testing environment.
Creating diagnostic tools offers an additional layer of assurance. Validating the repeatability of tests is crucial to minimize variation in testing outcomes over time. Verifying that losses remain within specified limits is equally pivotal, guaranteeing accurate measurements. Apart from equipment-provided self-tests, designing a diagnostic board proves highly advantageous. This custom board facilitates multiple tests, validating the full functionality of test equipment by incorporating checks for opens, shorts, loads, attenuators, and even diverse Device Under Test (DUT) scenarios. This comprehensive approach ensures that the equipment operates optimally across its spectrum of capabilities. Concluding this process with a validation using a “golden unit” certifies that the equipment is performing accurately and up to the expected standards.
Conclusion:
In the dynamic realm of RF power correlation, the amalgamation of proactive measures has emerged as the cornerstone for achieving unparalleled efficiency and precision. From embracing preventive maintenance and diagnostic tools to maintaining a meticulous calendar for equipment calibration, each practice contributes to the seamless orchestration of RF power testing. As we wrap up our exploration of good practices in RF power correlation, the resounding theme is clear: a disciplined approach to maintenance, diagnostics, and calibration is paramount. By adopting these strategies, organizations can not only minimize downtime and prevent equipment damage but also elevate the reliability and accuracy of their RF power testing environments. In this ever-evolving landscape, the commitment to best practices becomes the linchpin, ensuring that RF power correlation remains a beacon of accuracy in the face of technological advancement.
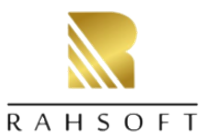
Learn more about this topic by taking the complete course ‘Introduction to RF Testing Fundamentals and RF Test Architecture – RAHRF412’. Watch the course videos for more detailed understanding. Also checkout other courses on RF system and IC design on https://rahsoft.com/courses/. Rahsoft also provides a certificate on Radio Frequency. All the courses offer step by step approach.